Spray guns are essential tools designed to atomize liquid substances, commonly paint. By using a spray gun, the painting process becomes more efficient, practical, and results in higher quality finishes compared to traditional manual methods like brushes. Additionally, spray guns significantly save on paint usage.
To achieve optimal results with a spray gun, it’s crucial to practice and hone your skills. Here are the five common types of spray guns available on the market, plus an innovative new product from Krigsmann Kroma.
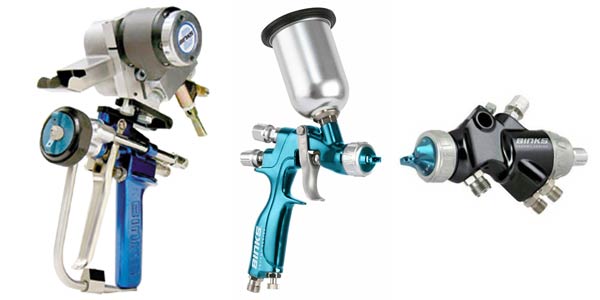
1. HVLP Spray Gun
High Volume Low Pressure (HVLP) Spray Gun
The HVLP spray gun is designed to minimize overspray, which is common with conventional spray guns. While conventional spray guns use high air pressure with low atomization, HVLP spray guns use lower air pressure, typically around 0.05 to 0.1 MPa (7–14 psi), to achieve better atomization.
Advantages of HVLP Spray Guns:
- Paint Efficiency: Up to 60-80% paint efficiency.
- Versatile Applications: Suitable for varnishing wood, metallic body painting, and enameling.
- Low VOC Waste: Reduces volatile organic compound (VOC) emissions.
Disadvantages of HVLP Spray Guns:
- Limited to Low Viscosity Paints: Not suitable for high-viscosity liquids.
- Potential for Rapid Wear: May wear out quickly with high-viscosity paints.
- Low Liquid Delivery Speed: Slower application rates.
2. Gravity Spray Gun
The Gravity spray gun differs from the HVLP spray gun by positioning the paint cup on top. It operates with low volume low pressure, an evolution of HVLP technology. This type of spray gun can handle high-viscosity materials and is suitable for finishes like sealers and top coats, except stains.
Advantages of Gravity Spray Guns:
- Handles High Viscosity: Suitable for various finishing materials.
- Consistent Application: Offers even coverage.
Disadvantages of Gravity Spray Guns:
- Lower Speed: Not ideal for large-scale furniture projects.
3. Airless Spray Gun
Airless Spray Gun
Airless spray guns provide an alternative method for painting by using high pressure to atomize the paint. This method results in the paint being forced through a small orifice, leading to a high-efficiency transfer rate of up to 70%.
Advantages of Airless Spray Guns:
- High Transfer Efficiency: Less overspray and more paint on the target surface.
- Ideal for Thick Paints: Can handle high-viscosity materials well.
4. Air Assisted Airless Spray Gun
Air Assisted Airless Spray Gun
This type of spray gun is a hybrid of airless and conventional air spray guns. It uses high-pressure air to improve atomization quality, making it ideal for topcoat applications.
Advantages of Air Assisted Airless Spray Guns:
- Superior Finish Quality: Enhances the atomization process for a smooth finish.
5. Suction Feed Spray Gun
Suction Feed Spray Gun
The Suction Feed spray gun features a paint cup located below the gun, drawing the paint up through suction.
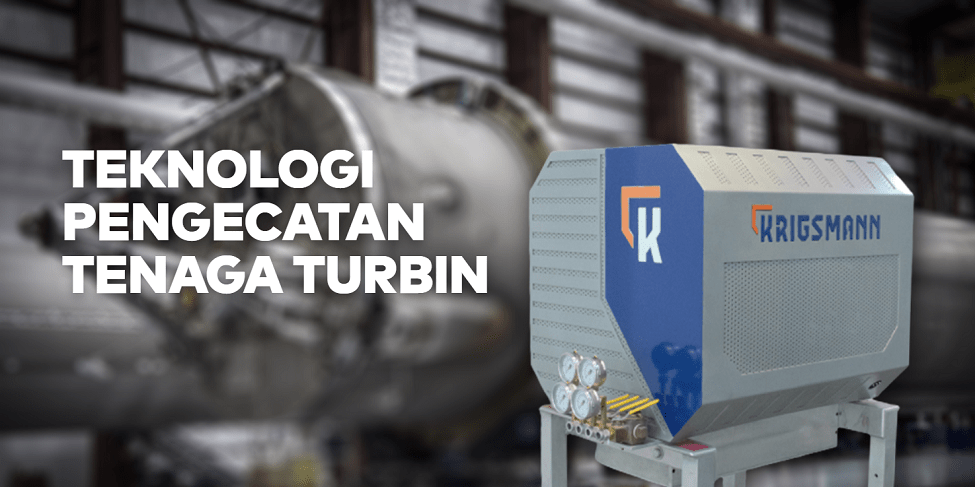
6. Krigsmann Kroma
Krigsmann Kroma: The Next Generation of Spray Guns
Krigsmann Kroma is an innovative spray gun technology developed in the US and further enhanced by Ford Motor Company. Now available in Indonesia, it aims to revolutionize the painting industry with its impressive paint efficiency of up to 90% and paint consumption savings of up to 70%.
Advantages of Krigsmann Kroma:
- High Paint Efficiency: Up to 90%.
- Significant Paint Savings: Up to 70% less paint consumption.
- Energy Efficient: Operates without requiring high pressure.
- Clean Air Output: Produces clean air without oil and water residues, reducing defects.
- Smooth Finishes: Delivers exceptionally fine and smooth paint jobs.
Why Choose Krigsmann Kroma:
- Efficient and Economical: Reduces overall paint and energy costs.
- Advanced Technology: Uses turbine technology instead of compressors.
- Environmentally Friendly: Clean air output with no harmful residues.
In summary, spray guns are a vital tool in achieving high-quality painting results. From HVLP to Krigsmann Kroma, each type offers unique benefits tailored to specific needs and applications. For the best results, consider your project requirements and select the appropriate spray gun technology.